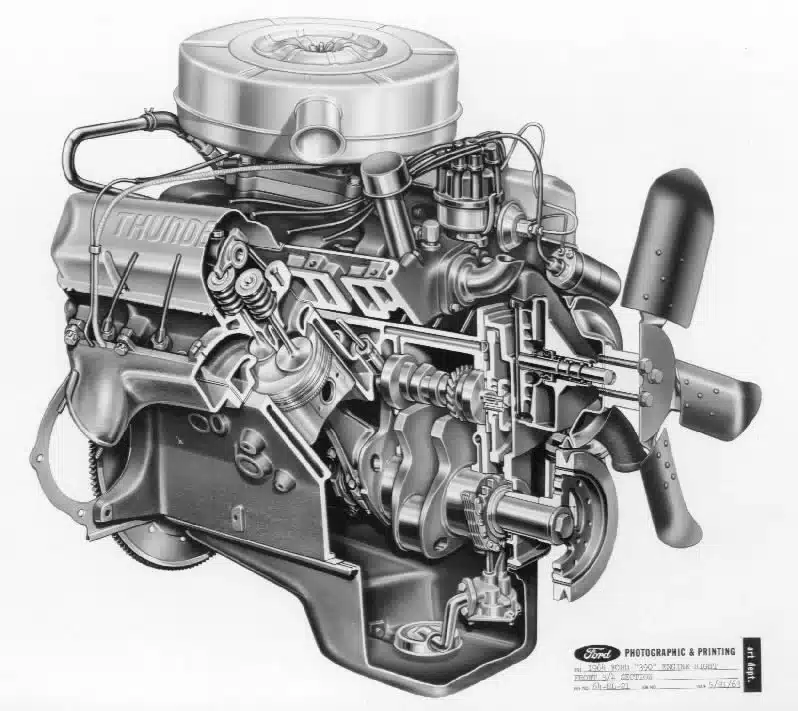
The FE (Ford-Edsel) engine family is a series of big-block engines produced by Ford Motor Company from 1958 to 1978. Known for their robust construction and versatility, FE engines have become iconic, leaving a lasting impact on the automotive industry. Initially designed for the new Edsel brand, the FE engine quickly became a staple for various Ford vehicles, transitioning seamlessly into the mainstream lineup. By the mid-1960s, the FE engine series had solidified its reputation, particularly in high-performance applications. Throughout its production run, the FE was used in some of Ford’s popular models, including the LTD, Galaxie, Mustang, and Torino as well as being used in light and medium-duty trucks.
History of the FE Engine Family
After WWII, our American highway system changed dramatically. Influenced by the Autobahn road network he saw in Germany, President Dwight D. Eisenhower strongly advocated for an upgraded way for Americans to traverse the country. This resulted in improved highways and new Interstate roads, mandated by the Federal Aid Highway Act of 1956, creating a demand for bigger, more powerful cars and trucks. With this in mind, Ford developed the FE engine family and introduced the 332ci model in 1958 amidst their pursuit of a more robust alternative to its existing engine lineup.
Significance
The FE engine family played a substantial part in the muscle car era of the 1960s, providing the horsepower and torque that performance enthusiasts craved. Their versatility made them suitable for a range of applications, from daily drivers to high-performance track cars.
FE engines were integral to many motorsport successes, particularly drag racing where they dominated competitions. The 427 side-oiler became legendary for its power and reliability, making it a highly sought after platform for performance builds both on and off the track.
Advanced Technology for its Era
The FE engine family benefited from several technological advancements that distinguished it from earlier Ford engine models. One key development was using a shaft-style overhead valve (OHV) design, which allowed for improved airflow and higher RPM capabilities. This design facilitated more efficient combustion, leading to greater horsepower and torque. Additionally, advancements in metallurgy and block construction provided FE engines with enhanced durability and strength, allowing them to withstand higher stress and improve performance reliability. The introduction of higher compression ratios and more sophisticated carburetion systems, including dual-quad configurations, further optimized fuel and air mixture, contributing to the engines’ legendary performance.
Evolution of the FE
Over the years, the design and features of the FE engines evolved significantly in response to changing market demands and technological advances. Early models, such as the 332 and 352 cubic inch engines, set the foundation for performance, but as consumer expectations grew, so did engine capabilities. By the time Ford introduced the iconic 427 cubic inch engine, they had refined the FE family with larger bore sizes, increased stroke lengths, and improved valvetrain designs. Innovations in cooling systems and lubrication also emerged, allowing the FE engines to operate more efficiently under high-performance conditions.
Ford Ends FE Production
Despite their considerable strengths, the FE engine family faced several challenges and limitations, particularly regarding their overall weight, exhaust emissions, and fuel efficiency. The performance and horsepower that defined the FE engines often came at the cost of fuel economy, which became a notable concern during an era marked by the oil crisis. Caused largely by skyrocketing gasoline prices due to the OPEC embargo of 1973, consumer tastes shifted to smaller, more fuel-efficient vehicles. At the same time, new Federal government standards pressured the automotive industry to prioritize decreased carbon monoxide and other greenhouse gas emissions. Because of its design and original intent, the FE engine struggled to meet the stricter emission levels that were mandated. These challenges ultimately influenced the transition toward lighter and more fuel-efficient engine models in Ford’s lineup, which led to the discontinuation of the FE line.
Outlook
Ford FE engines represent a significant chapter in automotive history, arguably one of the best platforms from the muscle car era – at least according to Ford fans. From its original development to fill the need for larger, more powerful engines and its lasting legacy in motorsport and popular culture, the FE family remains a beloved choice among classic car enthusiasts and performance builders today. Even though production of the FE ended almost 50 years ago, many new performance parts have been developed over the last couple of decades. Some of these, including upgraded aluminum cylinder heads, electronic fuel injection kits, and retro-fit hydraulic roller camshafts are just a few of the newer products available to bring the performance of the FE up to 21st century standards.
Do you have a FE? Are you ready to restore or upgrade your piece of automotive history? Whether you’re restoring an old Galaxie convertible for cruising or getting your Mach 1 ready for the drag strip, give us a call (or request an estimate using our online form) to discuss your goals and learn about a combination of classic and modern components can help you tap into your favorite Ford engine’s full potential.
Ford-Edsel…. Who is Edsel?
The only child of Henry and Clara Ford, Edsel was involved in all aspects of the business. It is said that Henry had made the most popular car in the world (the Model T), but Edsel wanted to make the best car in the world. Edsel’s efforts led to increased elegance, safety, and variety of vehicles from the Model A through the creation of the Mercury Division to the launch of the Lincoln Continental. When Ford (the Motor Company, not the man) launched their new line of intermediate vehicles in 1956, the company named both the division and the engine family after Edsel.
An Abbreviated FE Timeline
(click each date to expand)
1958
- The first FE engine was a 332ci version for the Edsel vehicle program.
- 352, 390, and 406 ci versions quickly followed the 332
- 352s and 390s were installed in full-size cars such as the Galaxie.
- The 406 had a larger bore than the 390, solid-lifter cams and optional multiple carbs gave this version the performance edge.
1963
- The 427ci is released as the lead piece for Ford’s big-block racing program through 1969.
- The 427 features a larger bore, cross-bolted main caps, and better cylinder heads.
- The 427 was relatively low-production and often considered too high-strung for general sale.
- 427 Galaxie drag-race version – reduced weight (changes to sheet metal, interior parts, frame) – high-riser version of the engine.
- 427 SOHC “Cammer” was only sold over the counter, never in a production car, and became ineligible for NASCAR when the rules changed to ban special racing engines. Available with a single four-barrel carburetor or a dual four-barrel barb, it is estimated that fewer than 500 Cammers were built. While available, these engines were widely used in Top Fuel and Funny Car drag racing, they were the only real competitor to the much better-known Chrysler Hemi engine.
- Both center-oiler and side-oiler versions were offered.
1964
- The Fairlane Thunderbolt with 427 high-riser manifold had quarter mile times between 11.6-12 seconds in NHRA Super Stock racing [drag racing]
1965-1967
- The 427 is made available in limited production Fairlanes and the rare & competitive Shelby 427 Cobra.
1966
- The final year for the 352 and 410 variants
1968-1970
- 390 and 428ci versions produced for passenger cars
- 428 Cobra Jet package introduced with higher-performance parts including heads, cam, and intake – resulting in a reliably competitive build for NHRA Stock and Super Stock class racing.
1971-1976
- 360 and 390ci versions produced for pickups
1978
- Final year of production.
- FE engines were only installed in medium-duty trucks for commercial applications this final year.
Usage
FE engines were used in various Ford and Mercury vehicles throughout their production run. Popular applications included:
Passenger Cars
The FE family powered full-size Ford models like the Galaxie and Mercury Monterey.
Performance Vehicles
The high-performance variants of the FE engines graced models such as the Ford Mustang and the iconic 427 Shelby Cobra, making them a favorite among muscle car aficionados.
Racing
The engines were used extensively in NASCAR, Le Mans, and NHRA, showcasing their performance capabilities.
Trucks
The engines were prevalent in Ford’s truck lineup, offering the necessary torque and durability for towing and hauling.
Design Highlights
The Ford FE engine family is characterized by its robust design, including:
Block Construction
FE blocks are made from cast iron, providing durability and strength under high-stress conditions.
Displacement Options
The FE family includes a variety of displacements ranging from 332 to 428 cubic inches, catering to different performance needs.
Bore and Stroke
Most engines in the FE family featured a bore size between 4.00 to 4.13 inches and stroke lengths ranging from 3.30 to 3.98 inches.
Baril Engine’s Complete FE Engine Packages
Significant differences exist in what one engine rebuilder includes in a “Short Block” or “Long Block” from another. If you’re comparing quotes for your Ford FE, please look at the details, as Baril Engine includes more in our packages than many other engine builders.
In addition to individual component engine machine work options, Baril Engine offers three levels of engine rebuild packages:
- Short Block: Includes completely machining the block, rebuilding or replacing the engine’s rotating assembly (pistons, rings, connecting rods, crankshaft and bearing) and the camshaft and timing components (if applicable).
- Long Block (LB): Includes all the work in the SB level and adds a complete rebuild of the cylinder head, installation of the cylinder head, lifters, rocker arms, upper gasket set, oil pump, timing cover, water pump, thermostat, and adjusting of the valves.
- Ready-to-Run (RTR): Includes all the work in the SB and LB levels and adds many or all the components and parts required for the engine to be ready to run, including all accessories, external covers, intake manifolds, exhaust manifolds or headers, carburetion or EFI, ignition components, and more.
Baril Engine is a custom engine builder, so our engine packages can be tailored to each engine’s application and specific needs. Therefore, there can be considerable variation in the processes performed, the parts included, and the total cost from one engine project to the next. It is essential that we discuss and document within your estimate your engine’s history, any known issues, previous repairs, and your specific needs and goals. The more information you provide, the better positioned we are to meet and exceed your goals. We will provide a written estimate so you will know exactly what is and is not included in your engine package.
Baril Engine’s Machining, Rebuilding, and Assembly Services
Disassembly and Cleaning
A thorough and quality cleaning of the engine components is a time-consuming and labor-intensive job. However, we firmly believe it is our entire process’s foundation.
Disassembly and Cleaning details
- Disassembly of the engine and all its components.
- Initial cleaning of the components with a high temp spray wash process.
- Remove any remaining carbon or material from the parts using a variety of hand and pneumatic cleaning tools and processes.
Return to top of Machining, Rebuilding, and Assembly Services Section
Cylinder Head
[Available individually or as part of the LB & RTR packages.]
Cylinder Head Inspection details
- Magnaflux the cylinder head to identify any previously undetected cracks. Magnaflux Testing, also known as magnetic particle inspection, uses a magnetic field and an iron oxide powder or solution to identify surface cracks in metals. It is a time-proven and reliable method of identifying external cracks.
- Pressure testing the cylinder head, as the name suggests, uses air or hot water pressure to test the integrity of the internal coolant passages. With this test, we can find cracks in the head’s coolant passages, leaking frost plugs, and other defects that need to be addressed as a part of our rebuild process.
- Inspect the valves for stem wear, straightness, and if they have sufficient margin to allow grinding.
- Inspect the valve guides for wear and proper clearance.
- Inspect valve seats for wear and defects.
Cylinder Head Rebuilding Process details
- Resurface (mill) the cylinder head’s deck to ensure it is straight, flat, and has the proper finish.
- Grind the valves or replace as needed.
- Install new valve seats as needed and cut to produce three-angle valve seats.
- Remove & replace valve guides as needed.
- Replace valve springs with new.
- Assemble the cylinder head and complete the final inspection of the finished head to verify it meets all specifications.
Return to top of Machining, Rebuilding, and Assembly Services Section
Engine Block
[Available individually or as part of a complete engine rebuild package.]
Engine Block Inspection details
- Magnaflux the block to identify any previously undetected cracks.
- Inspect and measure each main journal bore with a dial bore gauge after torquing the main caps on to specification. This inspection allows us to see if any of the main journal bores need to be resized.
- Inspect the main housing bores to ensure they are round and true.
Engine Block Reconditioning Process details
- Bore and hone the cylinders as needed to achieve the proper size and crosshatch bore finish.
- Resurface (mill) the block’s top deck to ensure it is straight, flat, and has the proper finish.
- If the main housing bores are out of spec, align bore the block to correct.
- Install new cam bearings.
Return to top of Machining, Rebuilding, and Assembly Services Section
Connecting Rods
[Available individually or as part of a complete engine rebuild package.]
Connecting Rod Reconditioning Process details
- Connecting rod piston pin housing bore (small end): The piston pin bushing on the small end of the connecting rod is subject to wear over time. We recondition the piston pin end on each connecting rod by removing and replacing the pin bushing and honing it to fit the new piston pin to achieve the specified clearance.
- Connecting rod crankpin housing bore (big end): If a rod’s crankpin housing bore is found to be deformed or worn during our inspection, we resize the bore by cutting the cap, torquing the cap on to specification, and bore and hone the crankpin bore to the specified size and finish.
Return to top of Machining, Rebuilding, and Assembly Services Section
Crankshaft and Camshaft
[Available individually or as part of a complete engine rebuild package.]
Crankshaft and Camshaft Inspection details
- Liquid Magnaflux the crankshaft to identify any previously undetected cracks. Any crankshaft found to have a crack or defect is replaced.
- Inspect and test the journals to verify they meet or exceed the required hardness specification.
- Inspect the crankshaft for straightness and measure the size and profile of each journal to verify they are as specified.
- Inspect the camshaft to determine if it can be reused or needs to be replaced.
Crankshaft Reconditioning Process details
- If required, we grind the crankshaft after we have verified that oversized bearings are available.
- Polish all the crankshaft’s rod and main journals to their required finish.
- Final wash and inspection to ensure all oil galleys are clear of machining debris.
Return to top of Machining, Rebuilding, and Assembly Services Section
Engine Assembly
[Available as part of a complete engine rebuild package.]
Pre-Assembly Engine Inspection details
- It is the assembling technician’s responsibility to inspect all parts and verify that each meets specification. We trust but verify!
Engine Assembly details
- Our highly experienced engine builders assemble all our engines in our assembly department, which is sealed off from the remainder of our shop.
- Our engine assembly is a process that involves many detailed procedures that are executed in a specific order by our engine builders so that the completed engine meets our performance and reliability standards.
Return to top of Machining, Rebuilding, and Assembly Services Section
Additional Services
Balancing
- Crankshaft Balancing: This process ensures crankshaft counterweights properly offset the force provided by the rotation and reciprocation of the piston and rod assembly. A technician spins the crank on a specialized crankshaft balancing machine with bobweights attached to simulate the installation of pistons and rods. When the crankshaft comes to a spot, the balancer will tell the tech where weight needs to be added or removed from the crank.
- Engine Rotating Assembly Balancing: Externally balanced engines require balancing the entire crankshaft assembly with attached vibration dampers and flywheels or flexplate.
Engine Break-In
- If we build your engine to the Ready to Run stage, we also offer engine break-in services, ensuring your new engine is truly ready to drop in and go.
Return to top of Machining, Rebuilding, and Assembly Services Section